In today’s fast-paced and highly-competitive business environment, managing inventory effectively is more crucial than ever before. Organizations are constantly seeking ways to improve efficiency, reduce operational costs, and enhance customer experience. However, many organizations continue to rely on outdated, legacy inventory management solutions that hinder achievement of these goals. Legacy inventory management solutions, often built decades ago, may have served their purpose at one time, but they come with a range of pitfalls that organizations need to avoid. Here we explore the limitations of legacy inventory management systems and discuss how modernization can lead to more streamlined operations, improved decision-making, and better financial outcomes.
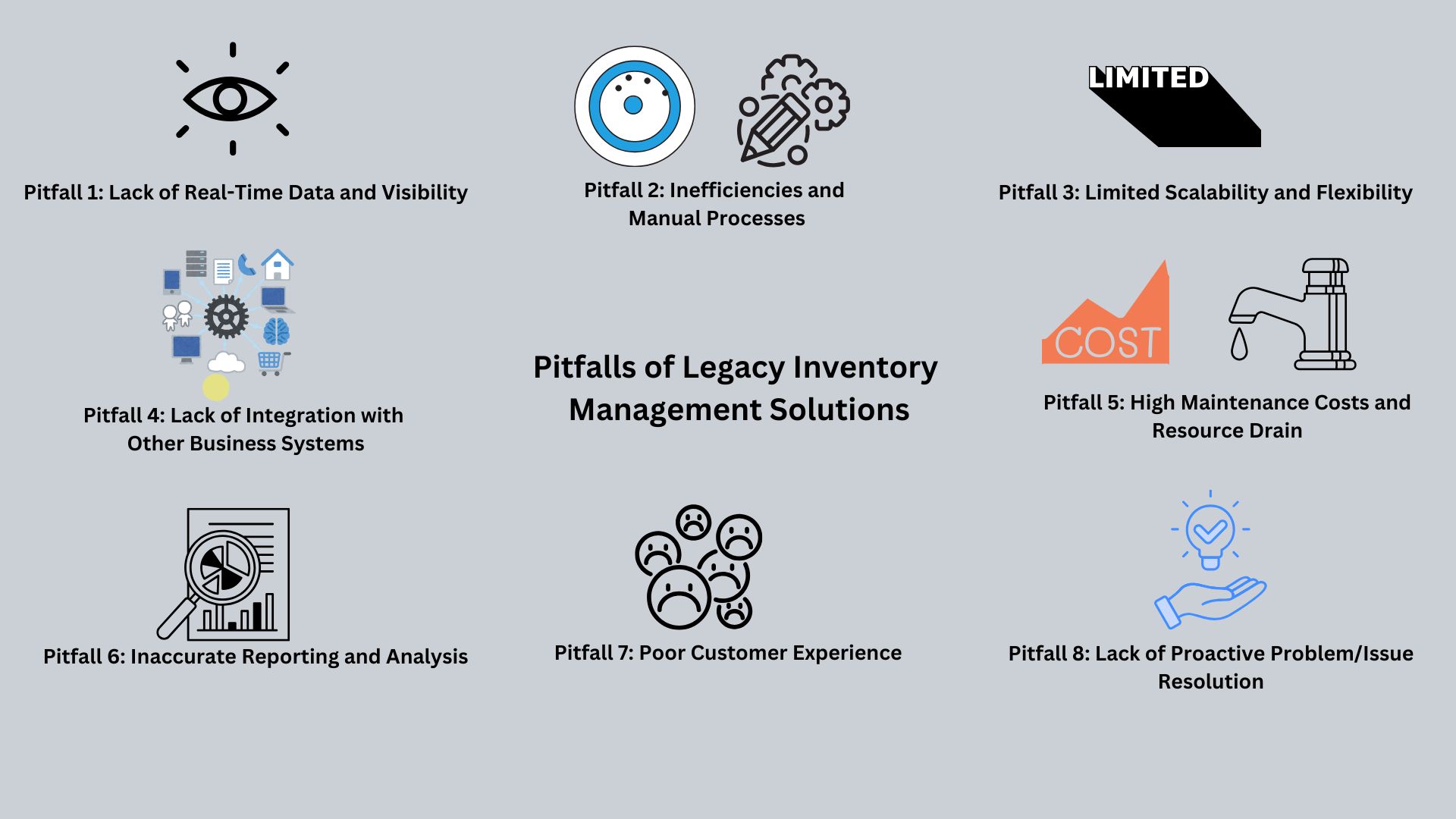
Pitfall 1: Lack of Real-Time Data and Visibility
One of the most significant drawbacks of legacy inventory management solutions is the inability to provide real-time data and visibility into inventory levels, orders, and stock movements. Many legacy inventory management solutions rely on batch processing, meaning inventory updates only occur at scheduled intervals, leaving organizations with outdated information.
Real-time data is essential for making informed decisions. An organization needs to know exactly how much stock is available, where it is located, and when it will be replenished to avoid stockouts, overstocking, or inefficiencies. Without this critical data, organizations risk losing sales, increasing operating costs, or damaging their reputation by failing to meet customer demands.
Solution: Modern inventory management solutions are cloud-based and provide real-time visibility, ensuring that organizations can track their inventory in real-time. Cloud-based solutions allow for integration with other parts of the business via APIs or pre-built connectors, such as order management, procurement, and sales, to further enhance efficiency and enable better decision-making.
Pitfall 2: Inefficiencies and Manual Processes
Legacy inventory management solutions often require manual data entry, leading to inefficiencies and the increased likelihood of errors. Inventory counts may need to be manually updated, leading to discrepancies between the actual stock and what is reflected in the system. This creates confusion, delays, and gaps that can have cascading effects on the business.
Solution: Automating inventory management process is one of the most effective ways to eliminate inefficiencies and reduce the likelihood of a human error. Modern inventory management solutions can automatically track inventory levels, update stock counts, generate purchase orders, and even forecast demand based on historical data. Automation not only saves time, but also helps to maintain accuracy across the entire operation.
Pitfall 3: Limited Scalability and Flexibility
As businesses grow and evolve, their inventory management needs become more complex. Legacy inventory management solutions, however, are often rigid and unable to scale to meet these new demands. Such solutions may struggle to accommodate multiple locations, international shipments, and complex supply chains.
When companies try to expand, they may find their legacy inventory management solutions are slow to respond and unable to handle large volumes of data or transactions. As a result, these systems limit an organization’s ability to scale efficiently, leading to operational bottlenecks and missed growth opportunities.
Solution: Modern inventory management solutions are designed to scale with your business. Cloud-based solutions allow companies to add new locations, integrate with global suppliers, and handle complex logistics with ease. With advanced functionality, such as multi-location tracking, automatic reorder points, and advanced reporting, these systems offer the flexibility needed to support growth without compromising performance.
Pitfall 4: Lack of Integration with Other Business Applications
Another issue with legacy inventory management solutions is their inability to integrate seamlessly with other business applications, such as accounting, sales, and customer relationship management (CRM). This siloed approach creates a fragmented view of business operations, making it difficult to make data-driven decisions or respond to customer needs in a timely manner.
For example, if an inventory management solution is not integrated with the sales system, there’s a high chance that sales teams may not have up-to-date information on stock availability, leading to over-promising and customer dissatisfaction. Similarly, without integration with accounting, businesses may struggle to reconcile inventory counts with financial records.
Solution: Modern inventory management solutions come with built-in integrations or APIs that connect seamlessly with other business systems. This integration enables a unified view of operations, allowing teams to collaborate more efficiently and respond faster to customer requirements. By connecting your inventory management solution with sales, accounting, and other departments, you ensure smoother workflows and better decision-making across the organization.
Pitfall 5: High Maintenance Costs and Resource Drain
Legacy inventory management solutions often require significant ongoing maintenance. Such solutions may be based on outdated technology that needs frequent updates, patches, and fixes. As the software ages, it can become increasingly difficult to find skilled professionals who can maintain and troubleshoot it, leading to costly downtime and extended disruptions.
In addition to maintenance costs, legacy inventory management solutions may require specialized hardware or on-premises infrastructure that adds to the overall cost of ownership.
Solution: Modern cloud-based inventory management solutions significantly reduce maintenance costs. As these y are hosted and maintained by the software provider, organizations don’t need to worry about infrastructure or frequent updates. This reduces the need for in-house IT support and allows your team to focus on strategic initiatives rather than dealing with technical or infrastructure issues.
Pitfall 6: Inaccurate Reporting and Analysis
Inaccurate or outdated reporting is another common pitfall associated with legacy inventory management solutions. These systems often lack the advanced reporting capabilities needed to analyze inventory performance, forecast demand, and identify trends. Without the ability to generate insightful reports and analytics, organizations may make poor decisions that lead to lost revenue or inefficiencies.
Solution: Modern inventory management solutions come with powerful reporting and analytics tools that help businesses track key performance indicators (KPIs), such as stock turnover rates, lead times, and order accuracy. With these insights, businesses can make data-driven decisions, optimize their inventory levels, and reduce waste.
Pitfall 7: Poor Customer Experience
Ultimately, the inefficiencies and inaccuracies associated with legacy inventory management solutions impact customer experience. Whether it’s delayed shipments, incorrect orders, or stockouts, customers are directly affected by the limitations of outdated systems.
A poor customer experience can result in lost sales, diminished brand loyalty, and negative reviews, which are harder to recover from.
Solution: Modern inventory management solutions help ensure that stock levels are optimized, orders are fulfilled on time, and customers receive the right products. By automating order processing, improving stock accuracy, and offering real-time tracking information, organizations can deliver a better customer experience and build long-term customer loyalty.
Pitfall 8: Lack of Proactive Problem/Issue Resolution
- Agentic Artificial Intelligence (Agentic AI):
- Agentic AI refers to systems that act autonomously, using machine learning (ML) and decision-making algorithms to manage inventory without human intervention. These AI agents can predict demand, optimize stock levels, and automate reorder processes based on real-time data.
- In inventory management, Agentic AI helps by improving forecasting accuracy, reducing human errors, and optimizing supply chain operations. It can decipher real-time adjustments to stock levels, respond to changes in demand patterns, and even handle complex scenarios, such as inventory shortages or surpluses, ensuring better inventory management and reducing waste or stockouts.
- Product Availability Readiness (PAR):
- PAR is the measure of how ready a company is to fulfill customer orders with available products in the stock. It focuses on ensuring that products are available in the right quantities and at the right time, minimizing the risk of stockouts or overstocking.
- In inventory management, maintaining high PAR ensures that businesses can meet customer demand consistently without delays. It improves efficiency, enhances customer satisfaction, and helps businesses stay competitive by ensuring a smooth and reliable supply of products.
Together, Agentic AI and PAR optimize inventory management by predicting and automating inventory decisions based on demand forecasts and product availability, ultimately enhancing operational efficiency and customer satisfaction.
Conclusion
To remain competitive, organizations must modernize their inventory management solutions to ensure they can meet the demands of the digital age. By moving to a cloud-based, integrated solution, companies can overcome the limitations of legacy systems, reduce costs, improve decision-making, and deliver a superior customer experience.
In the end, avoiding the pitfalls of legacy inventory management solutions isn’t just about adopting new technology – it’s about making a strategic investment in your business’s future growth and success. Are you ready to modernize your inventory management strategy? Discover how Pull Logic can drive better outcomes for your business today. Schedule a meeting here: https://pulllogic.com/contact/