How Effective Inventory Management Can Boost Your Lighting Business
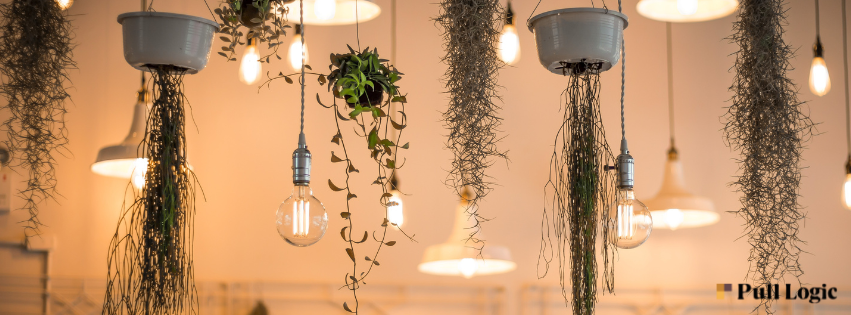
Effective inventory management is critical for any business, but for lighting manufacturers and retailers, it can be the difference between success and failure. This comprehensive guide will explore how optimizing your inventory processes can lead to increased efficiency, reduced costs, and higher customer satisfaction specifically within the lighting industry
Introduction
- Introduction
- Understanding Inventory Management in the Lighting Industry
- Benefits of Effective Inventory Management for Lighting Businesses
- Key Strategies for Inventory Optimization in Lighting
- Implementing Inventory Management Systems
- Best Practices in Inventory Management for Lighting Businesses
- Challenges and Solutions
- Future Trends in Inventory Management for Lighting Businesses
- Conclusion
Table of Contents
In the highly competitive lighting industry, managing inventory effectively can significantly boost your business performance. This involves ensuring that you have the right lighting components and fixtures available at the right time while minimizing costs and maximizing efficiency. This blog will delve into the importance of effective inventory management and provide actionable strategies to help your lighting business thrive.
Understanding Inventory Management in the Lighting Industry
Inventory management involves overseeing the flow of goods from manufacturers to warehouses and ultimately to customers. For lighting businesses, this means maintaining an optimal stock of various lighting products, including bulbs, LED panels, fixtures, control systems, and electrical components.
Key Components of Inventory Management
- Stock Levels: Maintaining the right amount of stock to meet customer demand without overstocking.
- Reorder Points: Determining when to reorder products to avoid stockouts.
- Lead Times: Understanding the time it takes for inventory to be replenished after an order is placed.
- Safety Stock: Keeping extra stock on hand to prevent stockouts during unexpected demand surges.
Benefits of Effective Inventory Management for Lighting Businesses
Improved Cash Flow
Efficient inventory management ensures that capital is not tied up in excess stock. By maintaining optimal inventory levels, businesses can free up cash to invest in other areas such as marketing, research, and development.
Enhanced Customer Satisfaction
Having the right products available when customers need them is crucial for maintaining high levels of customer satisfaction. Effective inventory management minimizes the risk of stockouts and ensures timely delivery, leading to happier customers and repeat business.
Reduced Holding Costs
Holding inventory incurs costs, including storage, insurance, and obsolescence. By optimizing inventory levels, lighting businesses can reduce these holding costs, thereby improving their bottom line.
Key Strategies for Inventory Optimization in Lighting
Demand Forecasting
Accurate demand forecasting is essential for effective inventory management. By predicting future demand for lighting products, businesses can plan their inventory more accurately, reducing the risk of overstocking or stockouts. Advanced techniques, such as AI and machine learning, can significantly enhance the accuracy of demand forecasts.
Just-In-Time (JIT) Inventory
JIT inventory management involves keeping inventory levels as low as possible by ordering goods only when needed. This strategy minimizes holding costs and reduces waste. However, it requires a reliable supply chain and accurate demand forecasting to be effective.
ABC Analysis
ABC analysis is a method of categorizing inventory based on its importance. Products are classified into three categories:
- A: High-value items with low sales frequency (e.g., specialized LED control systems).
- B: Moderate-value items with moderate sales frequency (e.g., standard lighting fixtures).
- C: Low-value items with high sales frequency (e.g., light bulbs and basic electrical components).
By focusing on managing ‘A’ items more closely, businesses can ensure that they invest more resources in the most critical inventory.
Implementing Inventory Management Systems
Implementing an inventory management system can automate many of the tasks involved in managing inventory, from tracking stock levels to generating reorder alerts. Modern systems often integrate with other business software, providing real-time data and analytics to support decision-making.
Choosing the Right System
When selecting an inventory management system, consider the following factors:
- Scalability: Ensure the system can grow with your business.
- Integration: Look for systems that integrate with your existing software.
- User-Friendliness: Choose a system that is easy to use and requires minimal training.
- Cost: Consider the total cost of ownership, including implementation and ongoing maintenance.
Best Practices in Inventory Management for Lighting Businesses
Conduct Regular Audits
Regularly auditing your inventory helps ensure accuracy in your stock records. This includes checking physical stock against inventory records to identify discrepancies and address them promptly.
Optimize Warehouse Layout
An optimized warehouse layout can significantly improve efficiency. Arrange your warehouse so that high-turnover items are easily accessible, reducing the time it takes to pick and pack orders.
Use Barcoding and RFID
Implementing barcoding and RFID (Radio Frequency Identification) technology can streamline inventory tracking and reduce human errors. These technologies provide real-time data on inventory levels and movements.
Develop Strong Supplier Relationships
Maintaining good relationships with your suppliers can help ensure a reliable supply chain. Strong supplier relationships can lead to better pricing, priority service, and faster resolution of issues.
Implement FIFO (First In, First Out)
Using the FIFO method ensures that older inventory is sold before newer stock. This is particularly important for products that have a limited shelf life or are subject to technological advancements.
Train Your Staff
Investing in staff training ensures that your team understands inventory management best practices and can effectively use your inventory management system. Well-trained staff can spot potential issues and suggest improvements.
Monitor Key Performance Indicators (KPIs)
Tracking KPIs such as inventory turnover ratio, order accuracy, and stockout rates provides valuable insights into the effectiveness of your inventory management processes. Use these metrics to identify areas for improvement.
Challenges and Solutions
Challenge 1: Demand Variability
Lighting businesses often face fluctuating demand due to seasonal trends or market changes. To mitigate this, use advanced forecasting techniques and maintain a safety stock for high-demand periods.
Challenge 2: Supply Chain Disruptions
Supply chain disruptions can lead to inventory shortages and delays. Diversify your supplier base and develop contingency plans to ensure a steady supply of products.
Challenge 3: Obsolete Inventory
Rapid technological advancements in the lighting industry can render products obsolete quickly. Regularly review inventory to identify slow-moving items and implement strategies to clear obsolete stock.
Future Trends in Inventory Management for Lighting Businesses
IoT and Smart Inventory Management
The Internet of Things (IoT) enables real-time tracking and monitoring of inventory, providing businesses with detailed insights into stock levels and movement.
AI and Machine Learning
AI and machine learning can enhance demand forecasting and inventory optimization, enabling more accurate predictions and efficient inventory management.
Sustainable Inventory Practices
Sustainability is becoming increasingly important. Implementing green inventory management practices, such as reducing waste and optimizing resource use, can enhance your business’s reputation and appeal to eco-conscious customers.
Conclusion
Effective inventory management is crucial for the success of lighting businesses. By implementing strategies such as demand forecasting, JIT inventory, and ABC analysis, and leveraging advanced inventory management systems, lighting manufacturers and retailers can improve cash flow, enhance customer satisfaction, and reduce holding costs. Staying abreast of future trends and overcoming challenges will ensure your business remains competitive in the dynamic lighting industry.
By prioritizing inventory management, you can ensure that your lighting business not only survives but thrives in the competitive market. To learn more about how effective inventory management can revolutionize your business, contact us today. Let us help you explore our solutions tailored to your business needs.