In today’s volatile global economy, supply chain disruptions are no longer occasional anomalies—they’re an ever-present reality. From the Trump-era tariffs that redefined international trade routes to the COVID-19 pandemic that paralyzed global logistics, and ongoing geopolitical tensions that threaten material access, the ability of businesses to adapt and respond has never been more critical. Among all the strategic pivots a company can make, resilient inventory management stands out as one of the most effective defenses against the unpredictable tides of disruption.
Understanding the Nature of Supply Chain Disruptions
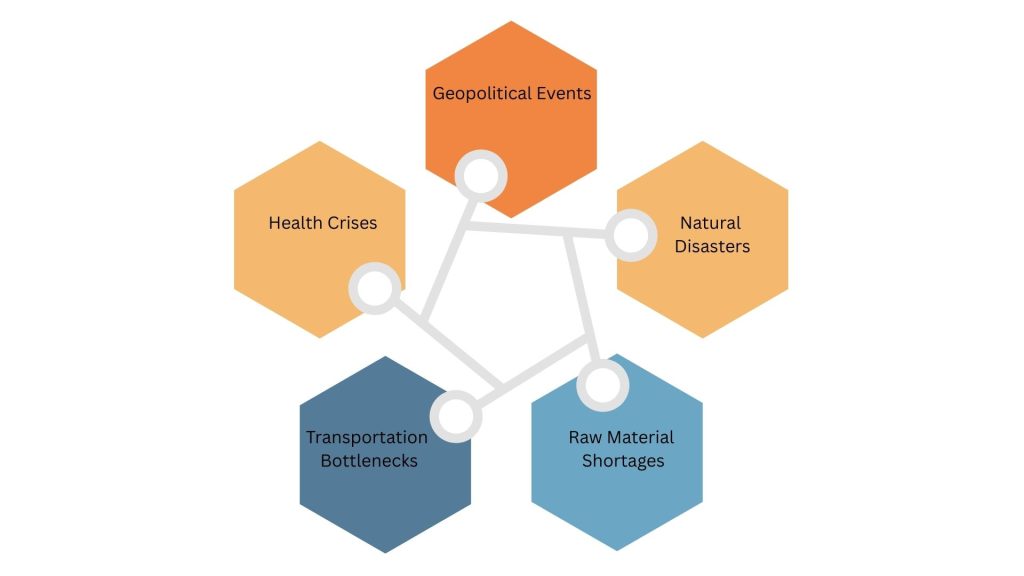
Supply chain disruptions refer to unexpected events that interfere with the normal flow of goods and materials. These disruptions can stem from a variety of sources:
- Geopolitical Events: Trade wars, sanctions, and political instability can drastically alter supply chain dynamics. For instance, the Trump administration’s imposition of tariffs on Chinese goods prompted many companies to rethink their sourcing strategies and shift operations to alternative countries like Vietnam and Mexico.
- Natural Disasters: Earthquakes, floods, hurricanes, and wildfires can shut down entire regions, crippling transportation networks and halting production lines.
- Health Crises: The COVID-19 pandemic revealed the fragility of just-in-time inventory systems. Lockdowns, workforce shortages, and border closures caused massive backlogs in global shipping and left shelves empty.
- Raw Material Shortages: Disruptions in the availability of key materials such as semiconductors, lithium, or even lumber can cascade through the supply chain, stalling production and impacting profitability.
- Transportation Bottlenecks: From port congestion to the Suez Canal blockage, even seemingly isolated events can create ripple effects that last for months.
Given this landscape, the question isn’t if disruptions will occur, but when. The solution? Building a resilient inventory strategy that can withstand these shocks.
Why Inventory Management Matters
Inventory serves as a buffer between supply and demand. When disruptions occur, a well-managed inventory can absorb shocks and maintain customer satisfaction. However, this balancing act is delicate:
- Overstocking leads to high carrying costs, spoilage, or obsolescence.
- Understocking results in stockouts, missed sales opportunities, and dissatisfied customers.
Resilient inventory management helps strike the right balance, ensuring operational continuity even when the external environment is unstable.
Core Strategies for Resilient Inventory Management
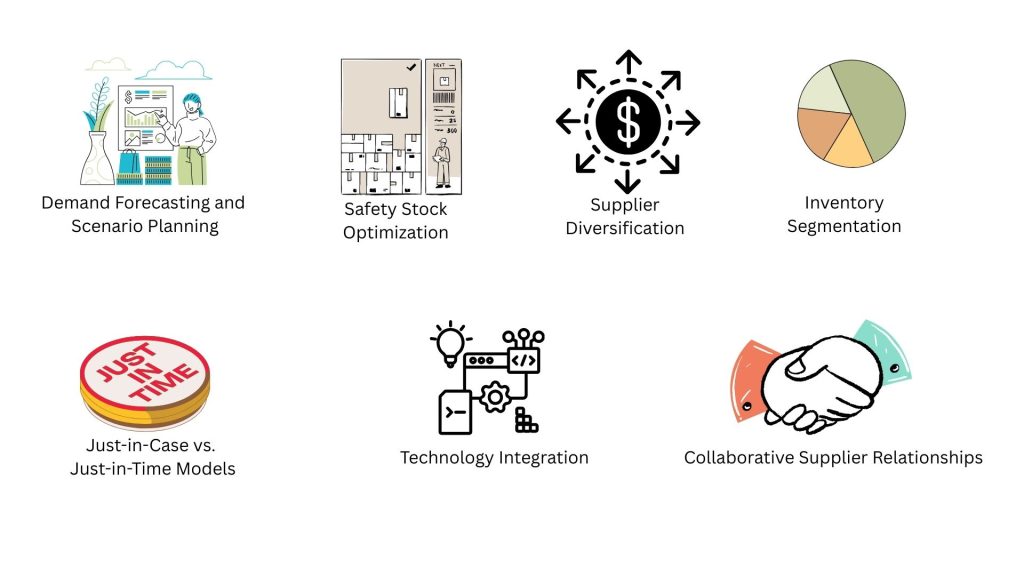
1. Demand Forecasting and Scenario Planning
Effective inventory management begins with accurate forecasting. Leveraging historical data, AI, and machine learning tools can help anticipate demand fluctuations with greater precision. Additionally, scenario planning allows businesses to simulate potential disruptions and model their impacts on inventory needs.
For example, a consumer electronics company might model the impact of a semiconductor shortage on its Q4 product launches and adjust procurement timelines accordingly.
2. Safety Stock Optimization
Safety stock is the extra inventory kept on hand to mitigate the risk of stockouts. However, the key is to optimize safety stock levels—not just inflate them. Businesses can use data analytics to determine the ideal safety stock based on lead time variability, demand volatility, and service level goals.
This approach minimizes excess inventory while still providing a cushion during disruptions.
3. Supplier Diversification
Over-reliance on a single supplier or region is a recipe for disaster. By diversifying the supplier base across different geographies, businesses can reduce their vulnerability to localized events.
Post-2018, many U.S. firms began sourcing components outside of China to avoid tariffs. This not only reduced costs but also improved their ability to adapt when China’s manufacturing hubs were hit hard by COVID-19.
4. Inventory Segmentation
All inventory is not created equal. Segmenting inventory based on factors like sales velocity, profit margin, or lead time allows companies to prioritize critical items. An ABC analysis, for example, categorizes inventory into:
- A: High-value, high-priority items (tight control, higher safety stock)
- B: Moderate value and demand
- C: Low-value, infrequent-demand items (looser control)
This approach helps focus resources where they matter most.
5. Just-in-Case vs. Just-in-Time Models
Traditionally, businesses leaned towards Just-in-Time (JIT) inventory to minimize holding costs. However, the pandemic exposed JIT’s limitations in a volatile environment.
In response, many companies are adopting a hybrid model that incorporates Just-in-Case (JIC) strategies—maintaining strategic reserves of critical items while still optimizing for efficiency. This blended approach helps balance cost and risk.
6. Technology Integration
Modern inventory management systems provide real-time visibility across the supply chain. Tools like IoT sensors, RFID tags, and cloud-based dashboards allow businesses to monitor stock levels, track shipments, and identify bottlenecks instantly.
Artificial Intelligence can also flag anomalies or predict delays before they occur, giving companies more time to respond proactively.
7. Collaborative Supplier Relationships
Strong partnerships with suppliers foster transparency, trust, and flexibility. Sharing sales forecasts, inventory levels, and disruption alerts enables joint decision-making and faster response times.
Vendor Managed Inventory (VMI) programs, where suppliers monitor and replenish stock based on agreed-upon metrics, can also enhance responsiveness and reduce administrative burden.
Real-World Lessons: Case Studies
- Toyota: Known for its lean JIT system, Toyota suffered a major setback in 2011 after the Tohoku earthquake disrupted parts supply. Since then, it has diversified suppliers and increased stockpiles of critical components.
- Apple: Despite global disruptions, Apple maintained product launches and relatively stable inventories through strategic partnerships, advanced forecasting, and vertical integration of key components.
- Peloton: During the pandemic, Peloton faced massive delivery delays due to demand spikes and supply constraints. Their over-reliance on overseas manufacturing and port delays forced them to invest heavily in air freight and eventually acquire domestic manufacturing capacity.
How AI presently drives Inventory Management:
- Walmart uses AI-driven inventory management to ensure product availability across thousands of stores. Their system analyzes historical sales data, weather patterns, local events, and customer behavior to predict demand for each product in each location. If a sudden weather change (e.g., an approaching storm) is detected, the AI system automatically increases inventory levels of essential items like water, batteries, and food in affected areas. Simultaneously, it adjusts restocking schedules and reroutes shipments to prevent stockouts or overstock. This real-time responsiveness helps Walmart stay resilient, reduce waste, and meet customer needs even during disruptions.
- Toyota uses AI to predict parts demand and manage global supply chain disruptions. Impact: During shortages (e.g., semiconductor chips), AI models help prioritize critical parts and adjust manufacturing schedules, ensuring continuity without overstocking.
- Amazon’s AI systems predict what products will be in demand in specific regions, enabling anticipatory shipping—sending items to distribution centers near likely buyers before orders are placed. Impact: Faster delivery, reduced holding costs, and better stock availability even during peak seasons.
Conclusion: Preparing for the Inevitable
Disruptions are inevitable, but being unprepared is not. Resilient inventory management empowers businesses to absorb shocks, maintain service levels, and recover faster. By leveraging technology, diversifying supply chains, and adopting smarter inventory strategies, companies can transform uncertainty into opportunity.
In a world where the next disruption is just around the corner, proactive inventory management isn’t just a tactical move—it’s a strategic imperative.
Call to Action
Is your inventory strategy ready for the next disruption? Start with a comprehensive audit of your current inventory practices, evaluate your supplier risk exposure, and explore advanced forecasting tools. The future may be uncertain, but with resilience built into your supply chain, your business doesn’t have to be. In order to navigate through these disruptions safely please schedule an appointment with one of our experts: https://pulllogic.com/contact/